सतह की तैयारी:
किसी भी धुंधला प्रक्रिया के प्रारंभिक चरण में, सतह दिखावा प्रदर्शन किया जाता है। यह सबसे अधिक समय लेने वाली और लंबी प्रक्रिया है, जिसे अक्सर ध्यान नहीं दिया जाता है, लेकिन जो उच्च गुणवत्ता वाले कवरेज प्राप्त करने के लिए एक शर्त है।
सतह की तैयारी निर्धारित करती है:
- गुणवत्ता,
- प्रतिरोध,
- कोटिंग की लोच और स्थायित्व,
- पेंट की सतह को पाउडर पेंट के इष्टतम आसंजन को बढ़ावा देता है
- और इसके विरोधी जंग गुणों में सुधार।
सतह से संदूषकों को हटाते समय, इस उद्देश्य के लिए उपयोग की जाने वाली सबसे उपयुक्त उपचार पद्धति और रचना को चुनना महत्वपूर्ण है। उनकी पसंद उपचारित सतह की सामग्री, प्रकार, संदूषण की डिग्री, साथ ही संचालन की शर्तों और शर्तों की आवश्यकताओं पर निर्भर करती है। धुंधला होने से पहले प्रारंभिक सतह के उपचार के लिए, ऑक्साइड फिल्मों को हटाने (अपघर्षक सफाई, नक़्क़ाशी) को हटाने और एक रूपांतरण परत (फॉस्फेटिंग, क्रोमेटिंग) का उपयोग किया जाता है।
इनमें से, केवल पहली विधि की आवश्यकता है, और बाकी का उपयोग विशिष्ट स्थितियों के आधार पर किया जाता है।
सतह की तैयारी प्रक्रिया में कई चरण शामिल हैं:
- सतह की सफाई और गिरावट;
- फॉस्फेटिंग (लोहा या जस्ता फॉस्फेट);
- रिंसिंग और फिक्सिंग;
- सुखाने कोटिंग।
पहले चरण में, उपचारित सतह की गिरावट और सफाई होती है। इसे यंत्रवत् या रासायनिक रूप से उत्पादित किया जा सकता है।
यांत्रिक सफाई के लिए, स्टील ब्रश या पीस डिस्क का उपयोग किया जाता है, और सतह के आकार के आधार पर, इसे विलायक के साथ नम कपड़े से साफ किया जा सकता है। रासायनिक सफाई को क्षारीय, अम्लीय या तटस्थ पदार्थों के साथ-साथ संदूषण के प्रकार और डिग्री, इलाज की सतह के प्रकार, सामग्री और आकार आदि के आधार पर उपयोग किया जाता है।
जब भागों की रासायनिक संरचना को संसाधित करना एक समाधान के साथ स्नान में डूबा जा सकता है या ब्लास्टिंग के अधीन हो सकता है (विशेष छेद के माध्यम से समाधान दबाव में आपूर्ति की जाती है)। बाद के मामले में, प्रसंस्करण दक्षता में काफी वृद्धि हुई है, क्योंकि सतह को यांत्रिक तनाव के अधीन भी किया जाता है, इसके अलावा, सतह के लिए एक स्वच्छ समाधान का एक निरंतर प्रवाह किया जाता है।
रूपांतरण उपलेयर का अनुप्रयोग नमी और दूषित पदार्थों को कोटिंग में प्रवेश करने से रोकता है, जिससे कोटिंग को छीलने और आगे नष्ट हो जाता है।
अकार्बनिक पेंट की एक पतली परत के आवेदन के साथ इलाज की सतह के फॉस्फेटिंग और क्रोमेटिंग, सतह के आसंजन ("आसंजन") को पेंट में सुधार करने में मदद करता है और जंग से बचाता है, इसके एंटी-जंग गुणों को बढ़ाता है। आमतौर पर, सतह को लोहे के फॉस्फेट (स्टील सतहों के लिए), जस्ता (गैल्वेनिक कोशिकाओं के लिए), क्रोमियम (एल्यूमीनियम सामग्री के लिए) या मैंगनीज, साथ ही साथ क्रोमिक एनहाइड्राइड के साथ इलाज किया जाता है। क्रोमियम या एनोडाइजिंग तरीकों का उपयोग अक्सर एल्यूमीनियम और इसके मिश्र धातुओं के लिए किया जाता है। जस्ता फॉस्फेट उपचार सबसे अच्छा जंग संरक्षण प्रदान करता है, लेकिन यह प्रक्रिया बाकी की तुलना में अधिक जटिल है। फॉस्फेटिंग पेंट के आसंजन को सतह से 2-3 गुना बढ़ा सकता है।
ऑक्साइड को हटाने के लिए (इनमें स्केल, रस्ट और ऑक्साइड फिल्में शामिल हैं), अपघर्षक सफाई (शॉट ब्लास्टिंग, शॉट ब्लास्टिंग, मैकेनिकल) और रासायनिक सफाई (नक़्क़ाशी) का उपयोग किया जाता है।
घर्षण कणों (रेत, शॉट), स्टील या कच्चा लोहे के कणिकाओं, साथ ही अखरोट के गोले का उपयोग करके सफाई की जाती है, जो संपीड़ित हवा की मदद से या केन्द्रापसारक बल द्वारा सतह पर उच्च गति से खिलाया जाता है। संक्षारक कण सतह से टकराते हैं, जंग या पैमाने और अन्य संदूषकों के साथ धातु के टुकड़ों को तोड़ते हैं। इस तरह की सफाई कोटिंग के आसंजन में सुधार करती है।
यह याद रखना चाहिए कि अपघर्षक सफाई केवल उन सामग्रियों पर लागू की जा सकती है जिनकी मोटाई 3 मिमी से अधिक है। बड़ी भूमिका निभाता है सही विकल्प सामग्री, क्योंकि बहुत बड़ा अंश सतह की एक बड़ी खुरदरापन को जन्म दे सकता है, और कोटिंग असमान रूप से चली जाएगी।
नक़्क़ाशी सल्फ्यूरिक, हाइड्रोक्लोरिक, फ़ॉस्फ़ोरिक, नाइट्रिक एसिड या कास्टिक सोडा के आधार पर नक़्क़ाशी वाले समाधानों का उपयोग करके दूषित पदार्थों, ऑक्साइड और जंग को हटाने है। समाधान में अवरोधक होते हैं जो पहले से साफ सतह क्षेत्रों के विघटन को धीमा कर देते हैं।
रासायनिक सफाई अपघर्षक की तुलना में अधिक उत्पादक और उपयोग करने में आसान है, लेकिन इसके बाद समाधान से सतह को धोना आवश्यक है, जो अतिरिक्त उपचार सुविधाओं के उपयोग की आवश्यकता है।
सतह की तैयारी के अंतिम चरण में, सतह के पारित होने का उपयोग किया जाता है, अर्थात्, क्रोमियम और सोडियम नाइट्रेट के यौगिकों के साथ इसका उपचार। पारितोषिक माध्यमिक क्षरण को रोकता है। इसका उपयोग सतह को कम करने और सतह को फॉस्फेट करने या क्रोमेट करने के बाद दोनों के लिए किया जा सकता है।
रिंसिंग और सूखने के बाद, सतह पाउडर कोटिंग के लिए तैयार है।
भागों को पूर्व-उपचार क्षेत्र छोड़ने के बाद, उन्हें रिंस किया जाता है और सूख जाता है। भागों को एक अलग भट्टी में या इलाज भट्ठी के एक विशेष खंड में सुखाया जाता है। सुखाने के लिए एक इलाज ओवन का उपयोग करते समय, सिस्टम का आकार कम हो जाता है, और अतिरिक्त उपकरणों का उपयोग करने की आवश्यकता नहीं होती है।
पाउडर कोटिंग:
जब भागों को पूरी तरह से सूख जाता है, तो उन्हें हवा के तापमान पर ठंडा किया जाता है। उसके बाद, उन्हें छिड़काव कक्ष में रखा जाता है, जहां पाउडर पेंट उन्हें लगाया जाता है। कक्ष का मुख्य उद्देश्य पाउडर कणों को कैप्चर करना है जो उत्पाद पर व्यवस्थित नहीं हुए हैं, पेंट का उपयोग करने और कमरे में प्रवेश करने से रोकने के लिए। यह एक फिल्टर सिस्टम और बिल्ट-इन क्लीनिंग एजेंट्स (जैसे डिब्बे, वाइब्रेटिंग स्क्रीन इत्यादि) के साथ-साथ सक्शन सिस्टम से लैस है। कैमरों को डेड-एंड और वॉक-थ्रू में विभाजित किया गया है। आमतौर पर छोटे आकार के उत्पादों को डेड-एंड चेंबर्स में चित्रित किया जाता है, और लंबे समय तक गुजरने वाले कक्षों में।
इसमें स्वचालित छिड़काव कक्ष भी होते हैं जिसमें पेंट को जोड़तोड़ करने वाली बंदूकों की मदद से सेकंड में लगाया जाता है। सबसे आम पाउडर कोटिंग विधि इलेक्ट्रोस्टैटिक छिड़काव है। यह एक वायवीय स्प्रे बंदूक का उपयोग करके एक ग्राउंडेड उत्पाद को इलेक्ट्रोस्टिकली चार्ज किया गया पाउडर है (इन्हें स्प्रे गन, गन और एप्लिकेटर भी कहा जाता है)।
कोई भी स्प्रेयर विभिन्न ऑपरेटिंग मोडों को जोड़ता है:
- वोल्टेज ऊपर और नीचे दोनों फैल सकता है;
- पेंट के प्रवाह (दबाव, जेट के प्रवाह) के बल को विनियमित किया जा सकता है, साथ ही साथ पाउडर की गति भी;
- नोजल के बाहर निकलने से भाग तक की दूरी बदल सकती है, साथ ही पेंट का कण आकार भी हो सकता है।
सबसे पहले, पाउडर पेंट को फीडर में डाला जाता है। हवा को दबाव में फीडर के छिद्रपूर्ण छिद्र के माध्यम से आपूर्ति की जाती है, जो पाउडर को निलंबित स्थिति में स्थानांतरित करता है, जिससे पेंट के तथाकथित "द्रवित बिस्तर" का निर्माण होता है। संपीड़ित हवा को कंप्रेसर द्वारा भी आपूर्ति की जा सकती है, जिससे "द्रवित बिस्तर" का एक स्थानीय क्षेत्र बनता है। फिर हवा का निलंबन एक हवा पंप (बेदखलदार) का उपयोग करके कंटेनर से लिया जाता है, एक कम एकाग्रता के लिए हवा से पतला और स्प्रेयर को खिलाया जाता है, जहां पाउडर पेंट घर्षण (घर्षण) के कारण एक इलेक्ट्रोस्टैटिक चार्ज प्राप्त करता है। यह निम्नानुसार होता है। चार्जिंग इलेक्ट्रोड, मुख्य बंदूक में स्थित, एक उच्च वोल्टेज की सूचना है, जिसके कारण एक विद्युत ढाल उत्पन्न होता है। यह इलेक्ट्रॉनों के पास एक विद्युत क्षेत्र बनाता है। इलेक्ट्रोड के चार्ज के विपरीत चार्ज ले जाने वाले कण इसकी ओर आकर्षित होते हैं। जब इस स्थान के माध्यम से पेंट कणों को चलाया जाता है, तो हवा के कण उन्हें एक विद्युत आवेश देते हैं।
संपीड़ित हवा का उपयोग करते हुए, चार्ज पाउडर पेंट एक न्यूट्रल चार्ज सतह पर गिरता है, बसता है और इलेक्ट्रोस्टैटिक आकर्षण के कारण उस पर रखा जाता है।
इलेक्ट्रोस्टैटिक छिड़काव दो प्रकार के होते हैं:
- कोरोनरी चार्ज के क्षेत्र में कण चार्जिंग के साथ इलेक्ट्रोस्टैटिक
- और ट्राइबोस्टेटिक छिड़काव।
इलेक्ट्रोस्टैटिक छिड़काव विधि के साथ, कण बिजली के बाहरी स्रोत (उदाहरण के लिए, एक कोरोना इलेक्ट्रोड) से एक चार्ज प्राप्त करते हैं, और एक ट्राइबोस्टेटिक के साथ, स्प्रेयर टरबाइन की दीवारों के खिलाफ उनके घर्षण के परिणामस्वरूप।
पेंट लगाने के पहले तरीके में, उच्च-वोल्टेज उपकरण का उपयोग किया जाता है।
पाउडर पेंट को चार्जिंग हेड के इलेक्ट्रोड और पेंट की जाने वाली सतह के बीच कोरोना डिस्चार्ज क्षेत्र में आयनित हवा के माध्यम से एक इलेक्ट्रिक चार्ज प्राप्त होता है। कोरोना डिस्चार्ज एटमाइज़र में एकीकृत एक उच्च वोल्टेज स्रोत द्वारा समर्थित है। इस पद्धति का नुकसान यह है कि जब इसका उपयोग किया जाता है, तो अंधा छेद और अवकाश के साथ सतहों पर पेंट लागू करना मुश्किल हो सकता है। चूंकि पेंट के कण पहले सतह के उभरे हुए हिस्सों पर जमा होते हैं, इसलिए इसे असमान रूप से दाग दिया जा सकता है।
ट्राइबोस्टेटिक छिड़काव के दौरान, पेंट को संपीड़ित हवा का उपयोग करके लागू किया जाता है और ढांकता हुआ के खिलाफ घर्षण के परिणामस्वरूप अधिग्रहीत चार्ज के कारण सतह पर रखा जाता है। अनुवाद में "ट्राइबो" का अर्थ है "घर्षण"। फ्लोरोप्लास्टिक का उपयोग एक ढांकता हुआ के रूप में किया जाता है, जिसमें से स्प्रे बंदूक के व्यक्तिगत हिस्से बनाए जाते हैं। ट्राइबोस्टेटिक छिड़काव के साथ, एक शक्ति स्रोत की आवश्यकता नहीं है, इसलिए यह विधि बहुत सस्ती है। इसका उपयोग जटिल आकार वाले भागों को रंगने के लिए किया जाता है। ट्राइबोस्टेटिक विधि के नुकसान में विद्युतीकरण की कम डिग्री शामिल है, जो इलेक्ट्रोस्टैटिक की तुलना में इसकी उत्पादकता को 1.5-2 गुना कम कर देता है।
कोटिंग की गुणवत्ता पेंट की मात्रा और प्रतिरोध, कणों के आकार और आकार से प्रभावित हो सकती है। प्रक्रिया की दक्षता भाग के आकार और आकार, उपकरणों के विन्यास, साथ ही पेंटिंग पर खर्च किए गए समय पर भी निर्भर करती है।
पारंपरिक रंगाई विधियों के विपरीत, पाउडर पेंट बिल्कुल खो नहीं जाता है, लेकिन स्प्रे चैम्बर रिकवरी सिस्टम में प्रवेश करता है और इसका पुन: उपयोग किया जा सकता है। कक्ष में, एक कम दबाव बनाए रखा जाता है, जो इससे पाउडर कणों के बाहर निकलने को रोकता है, इसलिए श्रमिकों द्वारा अभ्यास करने वालों की सांस की आवश्यकता गायब हो जाती है।
बहुलकीकरण:
उत्पाद के लिए लागू पाउडर रंग की रंगाई, पिघलने और पोलीमराइजेशन के अंतिम चरण में, पोलीमराइजेशन चैंबर में होता है।
पाउडर पेंट लगाने के बाद, उत्पाद को कोटिंग के गठन के चरण में भेजा जाता है। इसमें पेंट परत का पिघलना, कोटिंग फिल्म की बाद की रसीद, इलाज और शीतलन शामिल हैं। रिफ्लो प्रक्रिया एक विशेष रिफ्लो और पोलीमराइजेशन भट्टी में होती है। पोलीमराइज़ेशन चैंबर्स की कई किस्में हैं, एक विशेष उद्यम में उत्पादन की स्थितियों और विशेषताओं के आधार पर उनका डिज़ाइन भिन्न हो सकता है। उपस्थिति में, ओवन इलेक्ट्रॉनिक "भरने" के साथ सुखाने वाला कैबिनेट है। नियंत्रण इकाई का उपयोग करके, आप भट्ठी के तापमान को नियंत्रित कर सकते हैं, रंग भरने का समय और प्रक्रिया पूरी होने पर भट्टी को स्वचालित रूप से बंद करने के लिए टाइमर सेट कर सकते हैं। पोलीमराइजेशन भट्टियों के लिए ऊर्जा स्रोत बिजली, प्राकृतिक गैस और यहां तक \u200b\u200bकि ईंधन तेल हो सकते हैं।
भट्टियों को वॉक-थ्रू और डेड-एंड, क्षैतिज और ऊर्ध्वाधर, सिंगल और मल्टी-पास में विभाजित किया गया है। मृत-अंत भट्टियों के लिए, एक महत्वपूर्ण बिंदु तापमान वृद्धि की दर है। इस आवश्यकता के लिए वायु पुनर्चक्रण भट्टियां सबसे उपयुक्त हैं। विद्युत प्रवाहकीय कोटिंग के साथ डाइलेक्टर से बने अनुप्रयोग कक्ष भाग की सतह पर पाउडर पेंट का एक समान वितरण प्रदान करते हैं, हालांकि, यदि अनुचित तरीके से उपयोग किया जाता है, तो वे विद्युत शुल्क जमा कर सकते हैं और खतरनाक हो सकते हैं।
पिघलने और पोलीमराइजेशन 15-30 मिनट के लिए 150-220 डिग्री सेल्सियस के तापमान पर होता है, जिसके बाद पाउडर पेंट एक फिल्म (बहुलक) बनाता है। पोलीमराइजेशन चैंबर्स के लिए मुख्य आवश्यकता उत्पाद के एकसमान तापन के लिए एक स्थिर सेट तापमान (कम से कम 5 ° C का तापमान फैलने पर भट्ठी के विभिन्न भागों में रखने की अनुमति) को बनाए रखना है।
जब पाउडर पेंट की एक परत के साथ एक उत्पाद को एक भट्टी में गरम किया जाता है, तो पेंट के कण पिघल जाते हैं, एक चिपचिपा राज्य में जाते हैं और पाउडर पेंट की परत में हवा को विस्थापित करते हुए एक निरंतर फिल्म में विलय कर देते हैं। हवा का एक हिस्सा अभी भी फिल्म में बना रह सकता है, जिससे छिद्रों की गुणवत्ता में गिरावट आती है। छिद्रों की उपस्थिति से बचने के लिए, रंग को पेंट के पिघलने के तापमान से अधिक तापमान पर किया जाना चाहिए, और कोटिंग को एक पतली परत के साथ लागू किया जाना चाहिए।
उत्पाद के आगे हीटिंग के साथ, पेंट सतह में गहराई से प्रवेश करता है और फिर कठोर होता है। इस स्तर पर, संरचना, उपस्थिति, शक्ति, सुरक्षात्मक गुणों आदि की दी गई विशेषताओं के साथ एक कोटिंग बनाई जाती है।
धातु के बड़े हिस्सों को पेंट करते समय, उनकी सतह का तापमान पतली दीवारों वाले उत्पादों की तुलना में बहुत अधिक धीरे-धीरे बढ़ता है, इसलिए कोटिंग में पूरी तरह से कठोर होने का समय नहीं होता है, जिसके परिणामस्वरूप इसकी ताकत और आसंजन में कमी होती है। इस मामले में, हिस्सा पहले से गरम है या इलाज का समय बढ़ा दिया गया है।
कम तापमान पर और अधिक समय तक इलाज की सलाह दी जाती है। इस मोड के साथ, दोषों की संभावना कम हो जाती है, और कोटिंग के यांत्रिक गुणों में सुधार होता है।
उत्पाद की सतह पर आवश्यक तापमान प्राप्त करने के समय उत्पाद के द्रव्यमान और उस सामग्री के गुणों से प्रभावित होता है जिससे भाग बनाया जाता है।
इलाज के बाद, सतह को ठंडा किया जाता है, जो कन्वेयर श्रृंखला को लंबा करके प्राप्त किया जाता है। इसके अलावा, इस उद्देश्य के लिए विशेष शीतलन कक्षों का उपयोग किया जाता है, जो इलाज ओवन का हिस्सा हो सकता है।
कोटिंग बनाने के लिए उपयुक्त मोड को पाउडर पेंट के प्रकार, चित्रित किए जाने वाले उत्पाद की विशेषताओं, भट्टी के प्रकार, आदि को ध्यान में रखना चाहिए। यह याद रखना चाहिए कि तापमान पाउडर कोटिंग के लिए महत्वपूर्ण है, खासकर जब गर्मी प्रतिरोधी प्लास्टिक या लकड़ी के उत्पादों को कोटिंग करते हैं।
पोलीमराइजेशन के अंत में, उत्पाद को हवा में ठंडा किया जाता है। उत्पाद को ठंडा करने के बाद, कोटिंग तैयार है।
पाउडर कोटिंग्स के प्रकार
Epoxy पाउडर कोटिंग्स:
एपॉक्सी पाउडर का उपयोग किया जाता है जो कोटिंग की चिकनाई की एक उच्च डिग्री प्रदान करते हैं, आसंजन, लचीलापन और कठोरता की उत्कृष्ट विशेषताओं, साथ ही साथ रासायनिक हमले और सॉल्वैंट्स के प्रतिरोध।
मुख्य नुकसान कम गर्मी प्रतिरोध और प्रकाश प्रतिरोध हैं, साथ ही बढ़ते तापमान और बिखरे हुए दिन के प्रभाव के तहत पीले रंग के लिए एक स्पष्ट प्रवृत्ति है। ऐक्रेलिक पाउडर पेंट: व्यापक रूप से कोटिंग सतहों के लिए उपयोग किया जाता है; बाहरी उत्तेजनाओं के प्रभाव में, चमक और रंग जैसी विशेषताओं का संरक्षण करने की एक अच्छी डिग्री है, और गर्मी और क्षारीय वातावरण के लिए भी प्रतिरोधी है।
पॉलिएस्टर पाउडर कोटिंग्स:
सामान्य विशेषताएं एपॉक्सी और ऐक्रेलिक पाउडर के साथ मेल खाती हैं। इस तरह के पाउडर में पराबैंगनी प्रकाश के प्रभाव में पीलेपन के लिए उच्च शक्ति और उच्च प्रतिरोध होता है। वर्तमान में इमारतों पर उपलब्ध अधिकांश कोटिंग्स रैखिक पॉलिस्टर पर आधारित हैं।
इपॉक्सी और पॉलिएस्टर रेजिन युक्त हाइब्रिड पाउडर पेंट:
वे एक घटक के रूप में होते हैं एक विशेष पॉलिएस्टर राल का एक बड़ा हिस्सा (कभी-कभी 50% से अधिक)। इस तरह के संकर के गुण एपॉक्सी पाउडर के गुणों की याद दिलाते हैं, हालांकि, उनके अतिरिक्त लाभ को सुखाने के परिणामस्वरूप पीलेपन के प्रतिरोध में वृद्धि होती है और मौसम की स्थिति को सहन करने की क्षमता में सुधार होता है। हाइब्रिड पाउडर को वर्तमान में पाउडर पेंट उद्योग की नींव माना जाता है।
पॉलीयुरेथेन पाउडर पेंट्स: अच्छी शारीरिक और रासायनिक विशेषताओं का एक समान सेट है, और बाहर की तरफ अच्छी ताकत भी प्रदान करते हैं।
यह 150-220 डिग्री सेल्सियस के तापमान पर एक ओवन में उत्पाद के गर्मी उपचार (पोलीमराइजेशन) के बाद छिड़काव से गुजरता है। प्रौद्योगिकी को XX सदी के 60 के दशक में विकसित किया गया था और धातु संरचनाओं के प्रसंस्करण के लिए सक्रिय रूप से उपयोग किया जाता है।
विवरण पारित होने और गतिरोध के प्रकारों के छिड़काव में चित्रित किए गए हैं। पारंपरिक तरीकों के विपरीत, अतिरिक्त पाउडर पेंट अपरिवर्तनीय रूप से गायब नहीं होता है, लेकिन एक पुनर्प्राप्ति प्रणाली के माध्यम से पुन: उपयोग किया जाता है।
प्रौद्योगिकी के बुनियादी सिद्धांत
विधि एक संक्रमित तत्व की सतह पर संक्रमित पाउडर कणों के आकर्षण के सिद्धांत पर आधारित है। कणों को दो तरीकों से चार्ज किया जाता है: इलेक्ट्रो-और ट्राइबोस्टेटिक। पहले में एक निरंतर संकेत के साथ 20-100 केवी के वोल्टेज के तहत कोरोना इलेक्ट्रोड के साथ एक पीसी (पाउडर पेंट) की मजबूर चार्जिंग शामिल है, दूसरे में एक फ्लोराप्लास्टिक (गैर-दहनशील ढांकता हुआ) पर घर्षण द्वारा चार्ज कणों के साथ छिड़काव शामिल है।
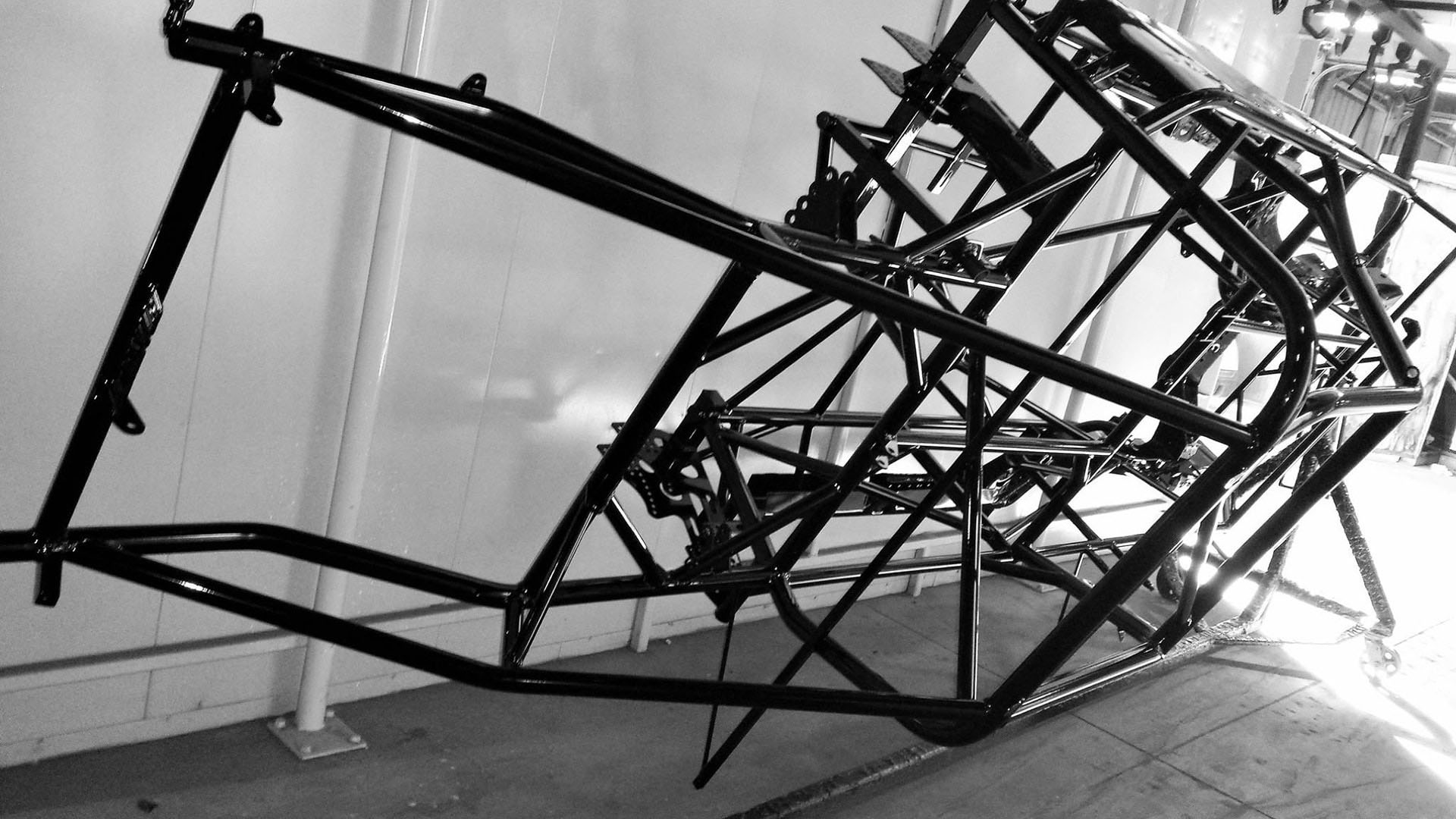
धातु संरचनाओं को चित्रित करने के लिए विधि की पसंद उत्पाद के आकार पर निर्भर करती है। इलेक्ट्रोस्टैटिक पेंटिंग विधि में, कण बल की रेखाओं के साथ चलते हैं, जिसके परिणामस्वरूप सपाट और घुमावदार सतहों पर पेंट की मात्रा में बड़ा अंतर होता है। इलेक्ट्रोड के वोल्टेज को कम करके और मशाल की दिशा को बदलकर समस्या को आंशिक रूप से हल किया जाता है।
ट्राइबोस्टेटिक विधि जटिल संरचनाओं के साथ अधिक कुशलता से काम करती है, लेकिन इसके लिए अधिक महंगी डाई या विशेष योजक की आवश्यकता होती है। दूसरी ओर, इस विधि में कणों के अवसादन का प्रतिशत एक कोरोना इलेक्ट्रोड के साथ चार्ज करने की तुलना में कम होता है। 60% से अधिक में एक बयान गुणांक संतोषजनक माना जाता है।
चित्रकला संरचनाओं के चरण
धातु संरचनाओं का पाउडर कोटिंग तीन चरणों में होता है:
- फाउंडेशन की तैयारी
- धुंधला हो जाना।
- बहुलकीकरण।
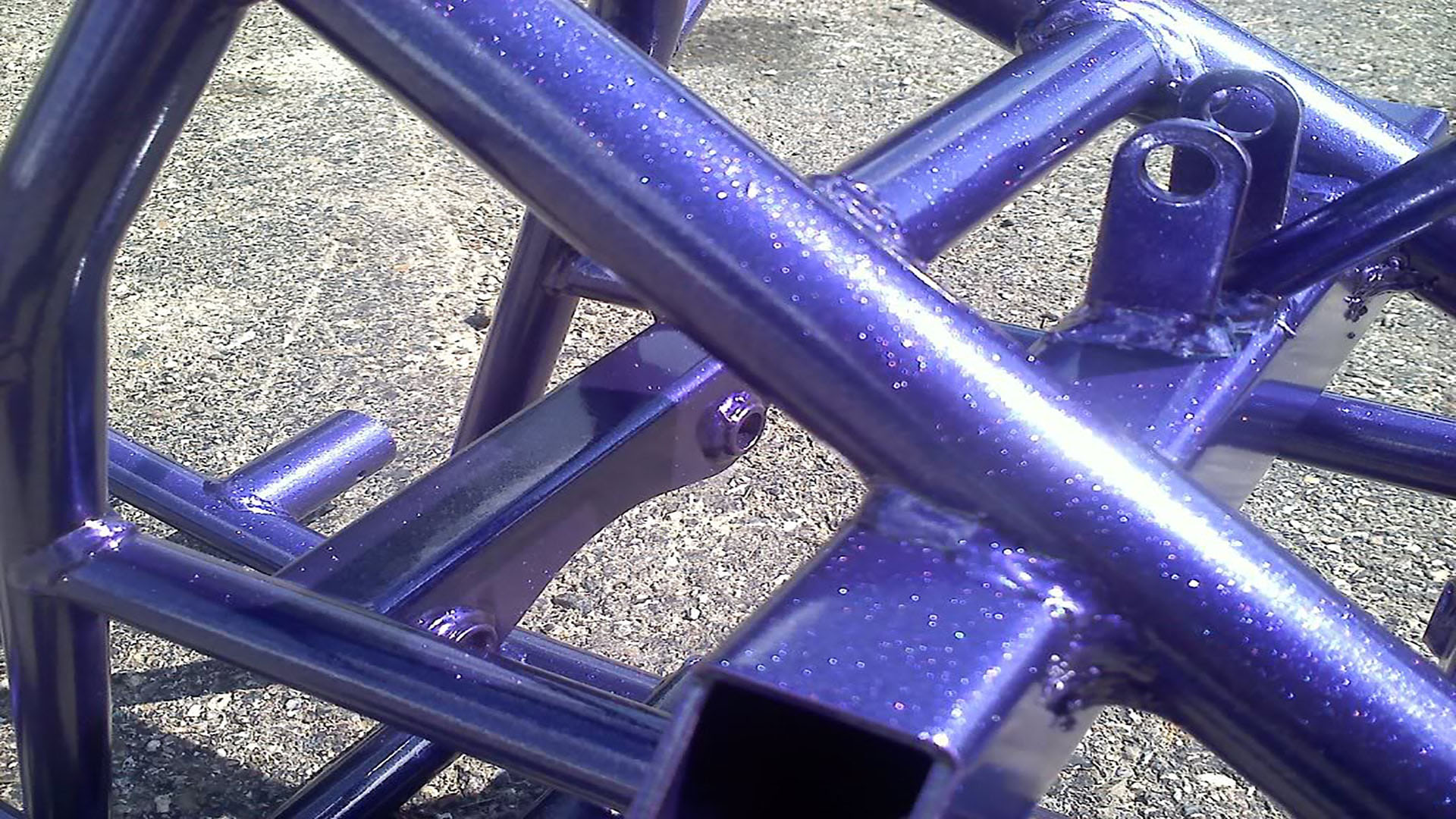
सतह की तैयारी
कोटिंग की गुणवत्ता सीधे पूरी सतह की तैयारी की डिग्री पर निर्भर करती है। नए भागों के लिए, यह कार्बनिक विलायक या जलीय केंद्रित-आधारित डिटर्जेंट समाधान के साथ गिरावट के लिए पर्याप्त है। छोटे बैचों को चित्रित करते समय पहली विधि उपयुक्त है, दूसरा - औद्योगिक संस्करणों के साथ। स्टील ब्रश या पीस डिस्क के साथ इस्पात संरचनाओं का पूर्व-उपचार।
लौह धातुओं की सतह से ऑक्साइड फिल्म और जंग उत्पादों को हटाने के लिए, फॉस्फोरिक और हाइड्रोक्लोरिक एसिड के समाधान का उपयोग किया जाता है। प्रभाव कम मात्रा में क्रोमिक एसिड के अतिरिक्त द्वारा बढ़ाया जाता है। धातु अचार को रोकने के लिए, एक एसिड जंग अवरोधक (1-2%) समाधान में जोड़ा जाता है। गैर-लौह धातु (एल्यूमीनियम, जस्ती इस्पात), इसके विपरीत, एक अम्लीय या क्षारीय वातावरण में आसंजन को बेहतर बनाने के लिए ऑक्सीकरण किया जाता है। इसके अलावा, लोहे के फॉस्फेट के साथ भाग के उपचार से आसंजन में वृद्धि की सुविधा होती है। इसी समय, सतह को पेंट के आसंजन का स्तर 2-3 गुना बढ़ जाता है।
बड़े संदूषकों के साथ, रेत, शॉट, स्टील छर्रों का उपयोग करके अपघर्षक सफाई का उपयोग किया जाता है। इस विधि का प्रदर्शन रासायनिक सफाई की तुलना में कम है, लेकिन इसके बाद सतह को धोने और सुखाने की कोई आवश्यकता नहीं है।
हार्डवेयर का रंग
यह एक विशेष कक्ष में कमरे के तापमान पर होता है जो एक वसूली और वायु सक्शन प्रणाली से सुसज्जित है। दो प्रकार के कैमरे हैं: डेड-एंड और वॉक-थ्रू। पहले मामले में, भागों को फास्टनरों पर लटका दिया जाता है और भट्ठी में ले जाया जा सकता है और दूसरे में - उन्हें एक सर्कल में पूरे कन्वेयर के माध्यम से, चित्रकार के अतीत के माध्यम से ले जाया जाता है।
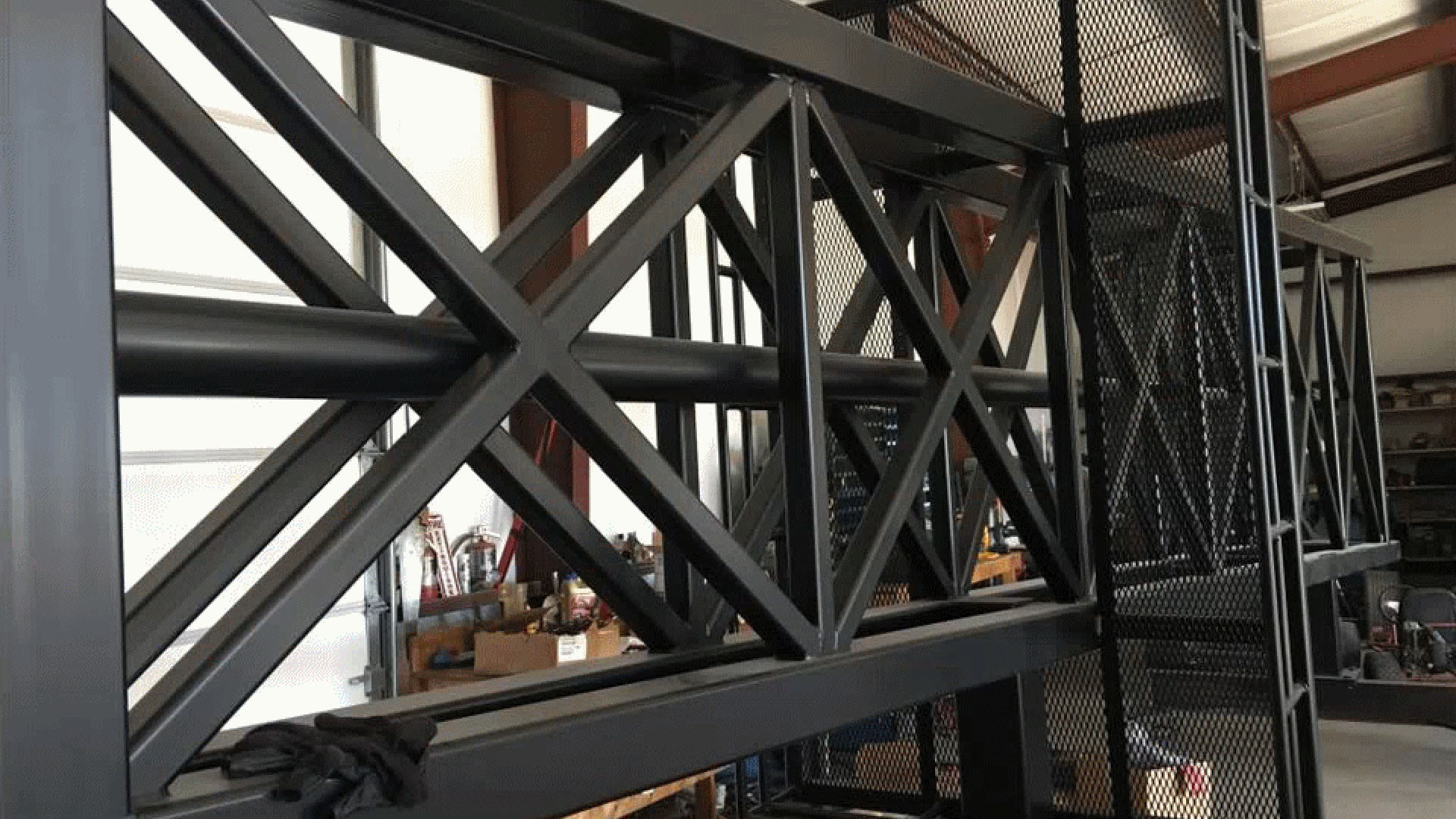
यह मैनुअल या स्वचालित प्रकार के वायवीय स्प्रेयर की सहायता से अपने आप चला जाता है। पाउडर को फीडर में डाला जाता है, जिसके बाद इसे संपीड़ित हवा के साथ झरझरा सतह पर आपूर्ति की जाती है। नतीजतन, एक निलंबन बनता है, जिसे एक बेदखलदार का उपयोग करके एटमाइज़र में पंप किया जाता है। इलेक्ट्रोस्टैटिक विधि में, रंग का विद्युत ढाल चार्ज इलेक्ट्रोड द्वारा निर्मित होता है, जबकि ट्राइबोस्टेटिक विधि में, यह एक ढांकता हुआ कणों के घर्षण द्वारा निर्मित होता है।
स्प्रे कोटिंग की गति और धातु संरचना (200-400 मिमी) की दूरी से आवश्यक कोटिंग की मोटाई प्राप्त की जाती है।
मोटाई कोटिंग के प्रकार पर निर्भर करती है:- सजावटी - 35-45 माइक्रोन।
- सुरक्षात्मक और सजावटी - 60-100 माइक्रोन।
- सुरक्षात्मक - 60-120 माइक्रोन।
पाउडर का पोलीमराइजेशन
धातु संरचनाओं का पाउडर कोटिंग एक बहुलककरण भट्ठी में समाप्त होता है। कदम में परत को पिघलाना, इलाज करना और ठंडा करना शामिल है। Reflow 150-220 ° C के तापमान पर होता है और औसतन 20-30 मिनट लगते हैं
तापमान पेंट के ब्रांड पर निर्भर करता है, साथ ही निर्माता पर भी। उत्पाद की वर्दी हीटिंग के लिए, भट्ठी में एक स्थिर (+/- 5 डिग्री सेल्सियस) तापमान बनाए रखना महत्वपूर्ण है। ऐसा करने के लिए, इसका डिज़ाइन हीटिंग ब्लॉक और एक वायु वितरण प्रणाली का उपयोग करता है।
पिघलने की प्रक्रिया एक फिल्म के एक साथ गठन और सतह में पेंट के प्रवेश के साथ हवा की छिड़काव परत से विस्थापन के साथ होती है। यदि भाग बड़ा है, तो इष्टतम प्रभाव के लिए पहले से गरम करना आवश्यक है। परत का इलाज समय भाग के द्रव्यमान और धातु की मोटाई पर निर्भर करता है।
धातु संरचनाओं के पाउडर कोटिंग के फायदे और नुकसान
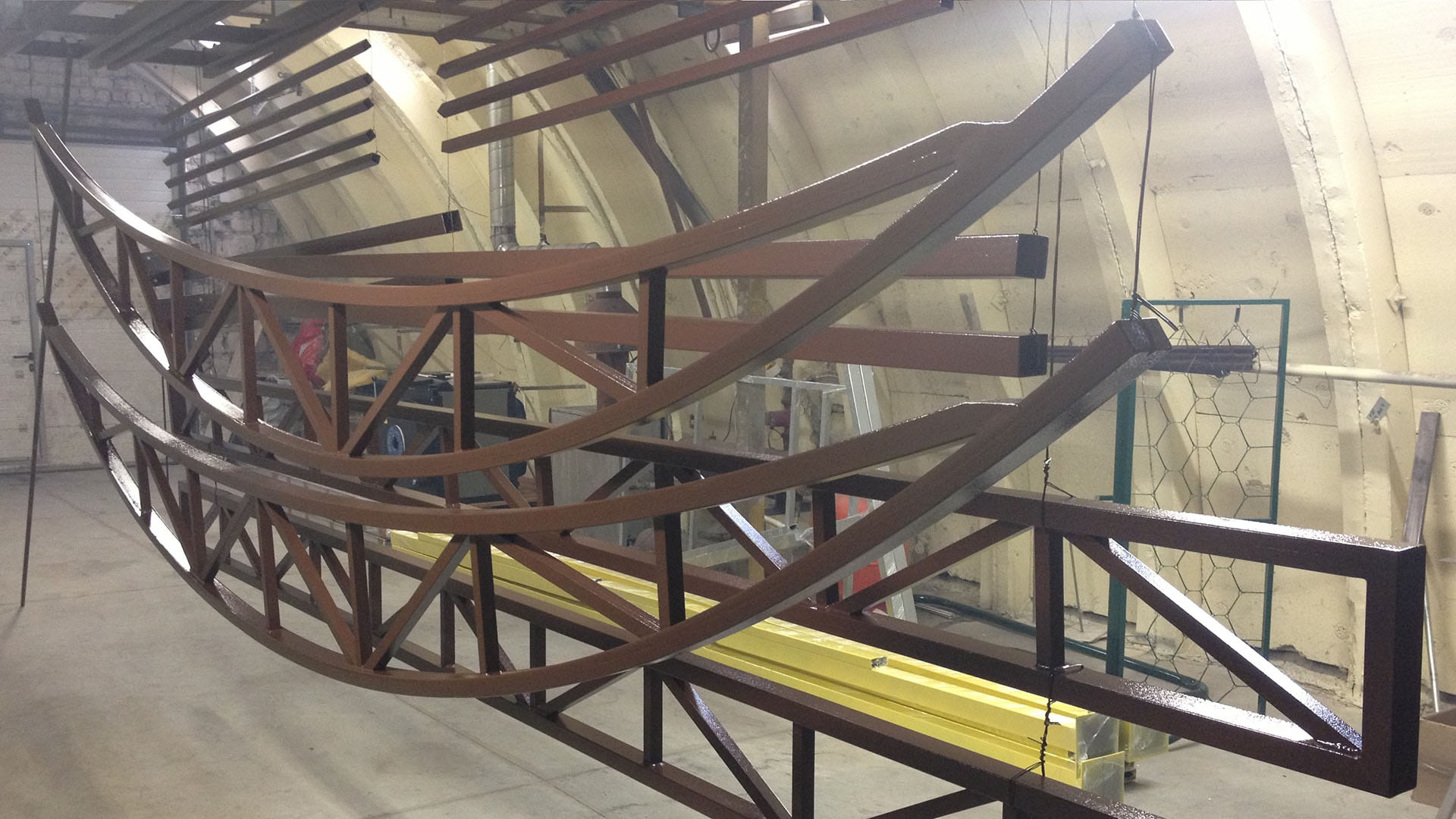
लागत बचत। सक्शन सिस्टम के लिए धन्यवाद, स्याही की हानि केवल 1-4% है।
स्वचालन की उच्च डिग्री उत्पादन, आप श्रमिकों को जल्दी से प्रशिक्षित करने की अनुमति देते हैं।
कोटिंग की उत्कृष्ट शक्ति और सजावटी गुण।
बहुमुखी प्रतिभा। इस पद्धति का उपयोग करके, किसी भी धातु संरचनाओं को चित्रित किया जाता है, जिसमें जटिल आकार के उत्पाद शामिल हैं।
इसी समय, संरचनाओं के पाउडर कोटिंग को केवल विशेष रूप से सुसज्जित कमरों में किया जाता है और पोलीमराइजेशन भट्ठी के आंतरिक आयामों तक सीमित होता है। पेंटिंग के दौरान उत्पन्न होने वाले स्थानीय दोषों को समाप्त नहीं किया जाता है - कुछ मामलों में, उत्पाद की पूरी पुनरावृत्ति की आवश्यकता होती है।
एक अन्य महत्वपूर्ण बारीकियों - बहुलक पेंट को तरल के साथ-साथ रंगा नहीं जाता है। अंतिम रंग प्रारंभिक चरण में बूट नुस्खा द्वारा निर्धारित किया जाता है और प्रक्रिया के दौरान इसे बदला नहीं जा सकता है। यह एक बल्कि समय लेने वाली प्रक्रिया है, जिसे स्पेक्ट्रोफोटोमीटर और उपयुक्त सॉफ्टवेयर की आवश्यकता होती है।
पाउडर कोटिंग के बारे में कुछ और उपयोगी लेख:
उपकरण और निर्माता का सही विकल्प।
- बड़ी लंबाई के धातु उत्पादों को धुंधला करने की तकनीक।
पॉलिमर पाउडर के साथ धातु संरचनाओं और विभिन्न उत्पादों को चित्रित करने की तकनीक पिछली शताब्दी के अंतिम दशक में विकसित की गई थी। औद्योगिक परिस्थितियों में, इस सदी की शुरुआत में पाउडर बहुलक कोटिंग का सक्रिय रूप से उपयोग किया जाने लगा।
कवरेज विकल्प
आज, अभिनव, नवीनतम तकनीकों के लिए धन्यवाद, बहुलक पाउडर के साथ कोटिंग के कई तरीके लागू होते हैं:
- इलेक्ट्रोस्टैटिक छिड़काव । इस पद्धति से धातु संरचनाओं और विभिन्न उत्पादों का पाउडर कोटिंग काफी मांग में है। इसकी तकनीक इस प्रकार है। एक विशेष एटमाइज़र का उपयोग करके, बहुलक के कणों को एक सकारात्मक विद्युत चार्ज के साथ चार्ज किया जाता है। पूर्व-अवक्षेपित सतह वाले उत्पादों को एक स्प्रे बूथ में रखा जाता है। इसमें, बहुलक पाउडर, एक वायवीय स्प्रे बंदूक का उपयोग करके, एक धातु संरचना या उत्पाद पर लागू किया जाता है। इलेक्ट्रोस्टैटिक तनाव के कारण, पेंट के कण चित्रित होने वाली उत्पाद की सतह का पालन करते हैं। चेम्बर की दीवारों पर चिपकने वाला पाउडर नहीं रहता है। यह समय-समय पर इसके नीचे स्थित एक विशेष रिसीवर में एकत्र किया जाता है, और पेंटिंग के लिए पुन: उपयोग किया जाता है।
पाउडर-लेपित धातु के हिस्सों को एक एयरटाइट कक्ष में रखा जाता है, जहां पाउडर को लगभग 200 डिग्री सेल्सियस के तापमान पर पॉलिमराइज़ किया जाता है। विवो में ठंडा होने के बाद, धातु संरचनाएं या भागों उपयोग के लिए तैयार हैं।
- दिशात्मक वायु प्रवाह का उपयोग करके पेंट लगाया जाता है। । एक निश्चित तापमान पर गर्म किए गए उत्पादों पर, एक स्प्रे बंदूक से एयरब्रश से बहुलक पाउडर के कण लगाए जाते हैं। एक गर्म सतह पर हो रहा है, पाउडर पेंट पिघला देता है, एक मजबूत, लेकिन पतली बहुलक फिल्म बनाता है। एक गुणवत्ता कोटिंग प्राप्त करने के लिए, धातु संरचनाओं के हीटिंग तापमान को यथासंभव सटीक रूप से निर्धारित करना आवश्यक है। उत्पादों की सतह और बहुलक कणों की बातचीत, पेंटिंग के क्षेत्र को भी ध्यान में रखना आवश्यक है। पोलीमराइजेशन प्रक्रिया को पूरा करने के लिए उत्पादों के अतिरिक्त गर्मी उपचार की आवश्यकता इस पद्धति का एक महत्वपूर्ण नुकसान है।
- वायु प्रवाह का उपयोग करते हुए इलेक्ट्रोस्टैटिक छिड़काव । यह विधि पहले दो बहुलक कोटिंग विकल्पों का सहजीवन है। पाउडर पेंट के कण पहले से विद्युत रूप से चार्ज किए गए दिशात्मक वायु प्रवाह का उपयोग करके धातु संरचना के पेंटवर्क सतह पर लागू होते हैं। उनके आंदोलन के दौरान, बहुलक भिन्न भी एक शुल्क प्राप्त करते हैं। कवर किए गए उत्पादों में एक तटस्थ विद्युत स्थिति होती है, जो जुड़े मैदान के लिए धन्यवाद। इलेक्ट्रिकल स्टैटिक्स की विधि द्वारा धातु संरचनाओं के पाउडर कोटिंग का उपयोग छोटे आयामों और सरल विन्यास वाले उत्पादों को कोट करने के लिए किया जाता है।
- लौ धुंधला हो जाना। उत्कृष्ट थर्मल प्लास्टिसिटी के साथ बहुलक के विकास के साथ लौ कोटिंग उपलब्ध हो गई है। पाउडर स्प्रे बंदूक, एक प्रोपेन बर्नर से सुसज्जित है। बहुलक के कण, आंच की एक धारा से गुजरते हुए, पिघल जाते हैं और अर्ध-तरल अवस्था में वर्कपीस की सतह पर छिड़के जाते हैं। चित्रकला की इस पद्धति के साथ एक पतली कोटिंग परत प्रदान की जाती है, जो कि वृद्धि की ताकत होती है। इस विधि का एक बड़ा प्लस उत्पाद को गर्म करने की आवश्यकता का अभाव है। नतीजतन, यह पहले से ही स्थापित पेंटिंग या विभिन्न सामग्रियों से बने बड़े आकार के ढांचे के लिए आदर्श है।
पाउडर कोटिंग के लाभ
बहुलक पाउडर लगाने के लिए उपयोग की जाने वाली आधुनिक तकनीक और उपकरण, एक अद्वितीय कोटिंग के साथ विभिन्न प्रकार की धातु संरचनाएं प्राप्त करने की अनुमति देता है। इसके आवेदन की महान लोकप्रियता बहुत सारे लाभों से जुड़ी है:
- आधार धातु की सतह को जंग के गठन से बचाने की गारंटी।
- बहुलक पाउडर के साथ लेपित उत्पादों में एक सुंदर और सौंदर्य उपस्थिति है। इस प्रौद्योगिकी का मुख्य लाभ आरएएल के विभिन्न रंगों में धातु संरचना की सतह को चित्रित करने का अवसर है।
- लागू पाउडर परत पूरी तरह से यांत्रिक तनाव, पराबैंगनी विकिरण, तापमान में अचानक परिवर्तन, उच्च आर्द्रता और आक्रामक वातावरण का विरोध करती है।
- पूर्ण गैर-विषाक्तता में मुश्किल। पर्यावरण सुरक्षा के कारण, इस पद्धति का उपयोग स्थायी उपयोग के लिए फर्नीचर के धातु तत्वों को चित्रित करने के लिए भी किया जाता है।
- आज यह औद्योगिक चित्रकला की सबसे नवीन और प्रगतिशील पद्धति है।
आवश्यक उपकरण
पाउडर कोटिंग करने के लिए, निम्नलिखित उपकरणों की आवश्यकता है:
- स्प्रे बूथ। यह धातु संरचनाओं में बहुलक पाउडर लगाने के लिए अभिप्रेत है। उत्पादों को विशेष स्प्रे बंदूक की मदद से लेपित किया जाता है जो कणों को पेंट करने के लिए एक इलेक्ट्रिक चार्ज को धोखा देते हैं। सभी कैमरे एक मार्ग प्रकार के बने होते हैं। एक ओर, यह उत्पाद को पेंट करने के लिए रोल करता है, दूसरी तरफ, एक लेपित धातु संरचना को आगे की प्रक्रिया के लिए रोल आउट किया जाता है। यह देखते हुए कि पाउडर अनुप्रयोग के दौरान बहुत अधिक धूल उत्पन्न होती है, सभी पेंट बूथ आधुनिक वेंटिलेशन सिस्टम से सुसज्जित हैं। बहुलक पाउडर लगाने की प्रक्रिया को मैन्युअल रूप से या स्वचालित रूप से नियंत्रित किया जा सकता है। यह कोटिंग की मात्रा और धातु संरचना के आयामों पर निर्भर करता है।
- चैंबर पोलीमराइजेशन कोटिंग। इसमें, उत्पाद की सतह पर उच्च तापमान के पॉलिमराइज़ के प्रभाव में पाउडर की एक जमा परत। स्थापित शक्तिशाली ताप तत्व कुछ ही मिनटों में चैम्बर स्थान को 230 0 C तक गर्म करते हैं। इस तापमान के प्रभाव में, पेंट के कण तरल अवस्था में पिघल जाते हैं। समान रूप से सतह पर फैलते हुए, वे एक पतली फिल्म बनाते हैं, जो ठंडा होने के बाद, ताकत में वृद्धि हुई है। प्रसार के कारण, बहुलक कणों को मजबूती से चित्रित करने के लिए संरचना की धातु से जुड़ा हुआ है। इस रासायनिक प्रक्रिया के लिए धन्यवाद, धातु संरचनाओं के पाउडर कोटिंग में वृद्धि हुई स्थायित्व की विशेषता है। कोटिंग के बहुलककरण की प्रक्रिया 60-30 मिनट के भीतर होती है।
- परिवहन उपकरण। ढके हुए धातु उत्पाद आमतौर पर भारी और अपेक्षाकृत भारी होते हैं। इसी समय, उन्हें सावधानी से ले जाया जाना चाहिए ताकि लागू पाउडर पेंट उनके आंदोलन के दौरान उखड़ न जाए। नतीजतन, विशेष ट्रॉलियां जो एक निलंबित मोनोरेल के साथ चलती हैं, धातु संरचनाओं के परिवहन के लिए उपयोग की जाती हैं। इन परिवहन उपकरणों पर, उत्पादों को पोलीमराइजेशन चैंबर से निकालने के बाद ठंडा किया जाता है।
पेंटिंग तकनीक
- सतह की तैयारी। धातु के साथ बहुलक कणों के उच्च-गुणवत्ता वाले आसंजन के लिए, उत्पादों से धूल, गंदगी, सुरक्षात्मक तेल निकालना आवश्यक है। लेपित होने वाली सतह को विभिन्न साधनों के साथ खराब होने की सलाह दी जाती है। ऐसी तैयारी धातु को पाउडर पेंट का उत्कृष्ट आसंजन सुनिश्चित करेगी। इसके कारण, लेपित मेटलवर्क में एक लंबी अवधि में एक ताजा चित्रित उपस्थिति होगी।
- पाउडर पेंट का अनुप्रयोग। एक परिवहन ट्रॉली पर तैयार उत्पाद को स्प्रे बूथ में लोड किया जाता है। एक विशेष बंदूक का उपयोग करके, धातु संरचना की सतह पर बहुलक पेंट लागू किया जाता है। इसमें, पाउडर के कणों को एक विद्युत आवेश प्राप्त होता है, जिसके कारण वे दृढ़ता से धातु का पालन करते हैं।
- बहुलकीकरण। बहुलक पेंट के साथ लेपित उत्पादों को एक कक्ष में रखा जाता है, जिसका आंतरिक स्थान कुछ ही मिनटों में लगभग 200 डिग्री सेल्सियस के तापमान पर लाया जाता है। गर्म होने पर, बहुलक परत पिघल जाती है और चिपचिपा हो जाता है। यह समान रूप से धातु संरचना की सतह पर फैलता है, आसंजन के कारण एक पतली लेकिन मजबूत परत बनाता है।
- ठंडा हो रहा है। चैम्बर को 40-60 0 C तक ठंडा करने के बाद, उत्पादों को इससे हटा दिया जाता है और उस स्थान पर परिवहन ट्रॉलियों पर रखा जाता है, जहां धातु की संरचनाएं प्राकृतिक परिस्थितियों में सामान्य तापमान तक ठंडी होती हैं।
मैकेनिकल इंजीनियरिंग, निर्माण और अन्य उद्योगों में महान मांग ने इस तथ्य को जन्म दिया है कि बहुलक पाउडर का उपयोग धातु भागों के परिष्करण के लिए सबसे प्रभावी विधि और टिकाऊ सामग्री के रूप में किया जाने लगा। आवेदन मुख्य रूप से एक मार्ग या मृत-अंत प्रकार के कक्षों में ट्राइबोस्टेटिक या इलेक्ट्रोस्टैटिक चार्जिंग की विधि द्वारा मैनुअल या स्वचालित स्प्रेयर द्वारा किया जाता है।
हम आपको पूरी उत्पादन तकनीक को अच्छी तरह से नहीं बता पाएंगे। लेकिन यहां आपको यह समझने की मूल बातें मिलती हैं कि यह कैसे किया जाता है। इसके अलावा, आप इस लेख में अतिरिक्त सामग्री के रूप में विषयगत वीडियो देख सकते हैं।
धारावाहिक और छोटे पैमाने पर उत्पादन में आवेदन की विशेषताएं
अनुप्रयोग प्रौद्योगिकी
- उत्पादन प्रक्रिया पर्यावरण के अनुकूल और पर्यावरण के अनुकूल है। उसी समय, उत्कृष्ट सजावटी और सुरक्षात्मक-सजावटी कोटिंग्स प्राप्त होते हैं। रचना को भाग की सतह पर वितरित किया जाता है, जिसे बाद में पाउडर पेंट पोलीमराइजेशन भट्टी में रखा जाता है। वहां, एक निश्चित तापमान पर गर्मी उपचार प्रक्रिया होती है।
- सामान्य रूप से कोटिंग का सिद्धांत इस प्रकार है: वर्कपीस को ग्राउंडेड किया गया है और चार्ज किए गए पेंट कण इसे आकर्षित करते हैं।
सामान्य तौर पर, पूरी प्रक्रिया को तीन चरणों में विभाजित किया जाता है, यह:
- भाग की तैयारी (सतह के उपचार);
- स्प्रे बंदूक से पाउडर का छिड़काव;
- लागू पाउडर का पुन: प्रवाह या पोलीमराइजेशन।
- परिष्करण भागों की गुणवत्ता, सबसे पहले, प्रत्येक चरण में प्रौद्योगिकी के सावधानीपूर्वक पालन पर निर्भर करेगी। इसके अलावा, निर्देश की आवश्यकता है कि कोई गड़गड़ाहट, प्रोट्रूडिंग वेल्ड, स्पलैश और जलने के साथ-साथ तेल और अन्य दाग नहीं हैं।
ट्रेनिंग
नोट। रासायनिक और यांत्रिक तरीकों का उपयोग आमतौर पर सतह से पुराने कोटिंग्स, पैमाने और जंग को हटाने के लिए किया जाता है।
यांत्रिक तरीकों में, सैंडब्लास्टिंग, शॉट ब्लास्टिंग और शॉट ब्लास्टिंग मशीनों का उपयोग करके ब्लास्टिंग और अपघर्षक उपचार है। और के रूप में degreasers जलीय क्षारीय और अम्लीय डिटर्जेंट समाधान, साथ ही कार्बनिक सॉल्वैंट्स का उपयोग किया जाता है।
यह देखते हुए कि कार्बनिक सॉल्वैंट्स जैसे कि व्हाइट स्पिरिट, 646 स्वास्थ्य के लिए हानिकारक हैं, उत्पादन निर्देश की सीमा एक सूती कपड़े से मैन्युअल रूप से कम होने पर पोंछती है और यह केवल छोटे बैचों पर लागू होती है।
बड़े बैचों को अपने हाथों से नहीं, बल्कि 40⁰C-60 .C के तापमान पर डिटर्जेंट रचनाओं के साथ घटाया जाता है। इस प्रक्रिया को 5-15 मिनट के लिए या 1-5 मिनट के लिए तरल में स्प्रे करके और धोने और सूखने के बाद भाग में होता है।
पाउडर आवेदन
आवेदन प्रक्रिया, जैसा कि ऊपरी तस्वीर में देखा जा सकता है, पाउडर छिड़काव कक्षों में किया जाता है, जहां कार्यशाला कक्ष () में कणों को रोकने के लिए हवा निकास और आकांक्षा प्रणालियां होती हैं।
मृत अंत कक्षों में, उत्पाद को एक विशेष विंडो के माध्यम से या केएन -2, केएन -5 के माध्यम से निलंबित और चित्रित किया जाता है, और अंश को केएन -3, केएन -6 के छिड़काव कार्य क्षेत्र के माध्यम से पारित चेंबर के माध्यम से चित्रकार के पास ले जाया जाता है। लंबे हिस्सों के लिए, डबल-एंट्री कैमरा KN-3-2, KN-6-2 (दो सिंगल-स्टेशन कैमरे एक दूसरे के विपरीत 180) घूमते हैं) हैं।
चूंकि डाई पॉलिमर के लिए है, यह स्वयं पाउडर है और आपको कुछ भी मिश्रण करने की आवश्यकता नहीं है, छोटे पैमाने पर उत्पादन के लिए, एक मैनुअल छिड़काव इकाई (यूआरएन -2) विकसित की गई थी। इसका एक फायदा है - पाउडर को उस मूल बॉक्स से आपूर्ति की जाती है जिसमें इसे कारखाने में पैक किया गया था, अर्थात इसे किसी भी कंटेनर में डालने की आवश्यकता नहीं है।
चूषण पाइप एक द्रवकरण उपकरण से सुसज्जित है, जो इंजेक्टर और हिल तालिका के साथ मिलकर उच्च आर्द्रता के साथ पाउडर के प्रसंस्करण की अनुमति देता है।
URN-2 को इलेक्ट्रोस्टैटिक और / या ट्राइबोस्टेटिक स्प्रे बंदूक से लैस किया जा सकता है। इसमें, अलग-अलग प्रकार की पेंट और अलग-अलग जटिलता की सतहों के लिए संयुक्त इकाई विकसित की गई थी। संयोजन आपको इलेक्ट्रोस्टैटिक मोड से ट्राइबो मोड में लगभग तुरंत स्विच करने की अनुमति देता है। इससे उत्पादन की दक्षता बढ़ जाती है और एक ही समय में, स्वाभाविक रूप से, निर्मित उत्पादों की कीमत गिर जाती है।
नोट। इलेक्ट्रोस्टैटिक विधि में एक कोरोना इलेक्ट्रोड का उपयोग करके कणों की मजबूर चार्जिंग शामिल है, जो उच्च वोल्टेज के तहत है। ट्राइबोस्टेटिक पद्धति में चार्जिंग कण शामिल होते हैं, क्योंकि वे एक ट्राइबेलेक्ट्रीली ट्राइबो-बैरल असेंबली (ट्राइबोफेक्ट) से गुजरते हैं।
फ्लैश बंद
पाउडर को उत्पाद पर लागू करने के बाद (यह बहुलक फर्श पेंट नहीं है), इसे परत पिघलाने के लिए एक कोटिंग बनाने के लिए पीपी -16 प्रकार की भट्ठी में भेजा जाता है।
फर्नेस भी डेड-एंड या वॉक-थ्रू होते हैं और इसमें हीट-इंसुलेटिंग पैनल, एक (डेड एंड) या टू (वॉक-थ्रू) डोर ब्लॉक होते हैं, साथ ही एयर रीसर्क्युलेशन सिस्टम के साथ एक से आठ हीटिंग ब्लॉक होते हैं। हीट-इंसुलेटिंग पैनल 100 मिमी मोटी बेसाल्ट प्लेटों से बना होता है जो जस्ती प्रोफाइल वाले पैनलों के बीच सैंडविच होती हैं।
ज्यादातर मामलों में, पाउडर पेंट के पॉलिमराइजेशन का तापमान + -5 -C की सटीकता के साथ 150 -C-180 withC और 10 से 20 मिनट की सामग्री समय है, हालांकि यह पाउडर निर्माता के निर्देशों पर निर्भर करता है। ये आवश्यकताएं वायु पुनर्चक्रण भट्टियों के लिए सबसे उपयुक्त हैं।
निष्कर्ष
यह ध्यान दिया जाना चाहिए कि ज़िंगा विद्युत प्रवाहकीय पेंट, साथ ही पॉलीस्टाइल धातु के लिए लौ मंद पेंट, भट्ठी में पोलीमराइजेशन से कोई संबंध नहीं है। रिफ्लो की प्रक्रिया विशेष रूप से पाउडर रंजक (
पाउडर पेंट से कोटिंग्स के उत्पादन के लिए एक विशिष्ट तकनीकी प्रक्रिया में तीन मुख्य चरण शामिल हैं: सतह की तैयारी, पाउडर सामग्री को लागू करना, इससे एक कोटिंग बनाना (बेकिंग)। कोटिंग्स की गुणवत्ता प्रक्रिया के सभी चरणों के तकनीकी शासनों के सख्त पालन पर निर्भर करती है। चित्र 4 विभिन्न प्रकार के पाउडर दिखाता है।
अंजीर। 4. पाउडर जो कोटिंग्स के रूप में उपयोग किया जाता है
बहुलक पाउडर कोटिंग्स के लाभ:
पर्यावरण के अनुकूल उत्पादन को व्यवस्थित करें;
95-98% पर सामग्री का उपयोग करें;
ऊर्जा लागत को 30-35% कम करें;
श्रम उत्पादकता को 1.5-2 गुना बढ़ाने के लिए;
सॉल्वैंट्स के उपयोग को हटा दें;
सतह को प्रारंभिक भड़काने के बिना करें;
विभिन्न विन्यास के उत्पादों पर एक समान कोटिंग मोटाई प्राप्त करें;
किसी भी जलवायु क्षेत्रों में कोटिंग्स का उपयोग करें, साथ ही साथ रासायनिक रूप से आक्रामक वातावरण में;
उत्पादों को आकर्षक, प्रतिस्पर्धी रूप देने के लिए रंगों की सतहों की विस्तृत श्रृंखला और बनावट का उपयोग करें। सब्सट्रेट (आसंजन), लोच, प्रभाव प्रतिरोध, विद्युत इन्सुलेशन विशेषताओं के साथ-साथ पहनने के लिए प्रतिरोध, एंटीकोर्सियन गुण भी तरल पेंट और वार्निश का उपयोग करते समय की तुलना में अधिक होते हैं। इलेक्ट्रोस्टैटिक क्षेत्र में पाउडर बहुलक पेंट के साथ पेंटिंग की प्रस्तावित तकनीक का उपयोग हमारे देश में और विशेष रूप से पारंपरिक पेंट और वैरिएबल कोटिंग्स के बजाय विदेशों में किया जाता है।
पेंटिंग से पहले उत्पाद की सतह तैयार करना (संक्षारण उत्पादों को कम करना और हटाना):
सतह की तैयारी की तकनीकी प्रक्रिया को निष्पादन की सटीकता पर अनुक्रमिक संचालन की एक श्रृंखला के रूप में दर्शाया जा सकता है, जो तैयार सतह की गुणवत्ता निर्धारित करता है।
प्रकटन नियंत्रण |
Obezzhi-rivanj |
गुणवत्ता नियंत्रण में कमी |
जंग हटाने * |
लावा निकालना |
Skladi- tion |
उत्पाद की सतह को खनिज तेलों या ग्रीस से घटाया जाता है।
थर्मल;
सॉल्वैंट्स या जलीय क्षारीय समाधान का उपयोग करना।
थर्मल विधि में, उत्पाद को गर्मी उपचार कक्ष में रखा जाता है, जहां, उच्च तापमान (250 - 300 डिग्री सेल्सियस) के प्रभाव में, उत्पाद की सतह से तेल फिल्में वाष्पित हो जाती हैं।
सॉल्वैंट्स या जलीय क्षारीय समाधानों के साथ घटता आमतौर पर उन धातुओं के लिए उपयोग किया जाता है जो जंग से डरते नहीं हैं। सतह को साफ करने के लिए पानी-क्षारीय विधि के रूप में, डिटर्जेंट एमएस -2 (20-25 ग्राम / लीटर तक सक्रिय योजक की एकाग्रता के साथ) के समाधान की सिफारिश की जाती है। वसा सामग्री के आधार पर, उत्पाद की सतह को यांत्रिक क्रिया (ब्रश, आदि) का उपयोग करके पानी-क्षारीय समाधान में धोया जाता है या नम, लिंट-फ्री कपड़े (समाधान में सिक्त और गलत तरीके से गीला) के साथ मिटा दिया जाता है, जिसके बाद उत्पाद सूख जाता है।
रूपांतरण कोटिंग्स के आवेदन का उद्देश्य उत्पादों की सुरक्षा में सुधार करना है, जिससे इसे और अधिक विश्वसनीय बनाया जा सके। लौह धातुओं और गैर-लौह के ऑक्सीकरण का सबसे आम फॉस्फेटिंग, मुख्य रूप से एल्यूमीनियम और इसके मिश्र। जब फॉस्फेटिंग, जस्ता युक्त फॉस्फेटिंग सांद्रता (KF-1, KF-3, आदि) सबसे अधिक बार उपयोग किया जाता है। फॉस्फेटिंग आमतौर पर जेट विधि द्वारा गीली सफाई इकाइयों में 50-60 डिग्री सेल्सियस के तापमान पर 1.5-2.5 मिनट के प्रसंस्करण समय के साथ किया जाता है। रासायनिक ऑक्सीकरण आमतौर पर क्रोमियम युक्त यौगिकों के साथ किया जाता है, इसलिए ऑपरेशन को क्रोमेशन कहा जाता है। सबसे व्यापक रूप से इस्तेमाल किए जाने वाले ध्यान केंद्रित अल्कॉन -1, अल्कॉन -1 के, और फॉर्मिख्रोम हैं। रासायनिक ऑक्सीकरण 20-30 डिग्री सेल्सियस पर किया जाता है, 5-30 एस की अवधि के साथ। ऑक्साइड कोटिंग्स की मोटाई आमतौर पर 1 माइक्रोन से अधिक नहीं होती है। रूपांतरण कोटिंग्स प्राप्त करने का अंतिम चरण, साथ ही गीली सतह की तैयारी के किसी भी संचालन, पानी से उत्पादों का सूखना है। इसे 110-140 ° C पर गर्म हवा के साथ उड़ाकर बाहर किया जाता है।
वायवीय इलेक्ट्रोस्टैटिक छिड़काव (एक ग्राउंड भाग के आसपास) द्वारा उत्पाद की सतह पर पाउडर पेंट का अनुप्रयोग:
उत्पाद की सतह पर एक बहुलक कोटिंग प्राप्त करने की तकनीकी प्रक्रिया में निष्पादन की सटीकता पर कई अनुक्रमिक संचालन शामिल हैं, जो परिणामी कोटिंग की गुणवत्ता पर निर्भर करता है।
सतह की स्थिति की निगरानी |
कोटिंग लागू सेट |
कोटिंग का गठन |
कोटिंग कूलिंग |
प्राप्त कोटिंग का गुणवत्ता नियंत्रण |
Skladi- tion |
न्यूमॉलेस्ट्रोस्टेटिक कोटिंग की विधि पाउडर सामग्री और उत्पाद की सतह के बीच के अंतर पर आधारित होती है, जब एक पैमाइश मात्रा में चार्ज पाउडर सामग्री उत्पाद की सतह पर पाउडर एयरोडाइस्पोर्ट के रूप में समान रूप से खिलाया जाता है।
सतह पर सही कोटिंग के लिए, उत्पाद को चित्रित करने के लिए एक एल्गोरिथ्म बनाया गया है, इस तथ्य से निर्देशित किया जाता है कि, सबसे पहले, कोटिंग को खांचे, जोड़ों, वेल्डिंग, टांका लगाने, जुड़ने आदि पर लागू किया जाता है, दूसरा, आंतरिक सतहों पर और तीसरा, अंतिम, बाहरी रूप से। (सामने) सतहों।
उत्पाद की सतह पर पाउडर सामग्री को लागू करने के लिए, उत्पाद और पीपीएम आवेदन कक्ष के बीच अच्छा संपर्क सुनिश्चित करना आवश्यक है, और जब कक्ष के बाहर कोटिंग, उत्पाद और जमीन।
कोटिंग नियंत्रण लागू करते समय:
एक मशाल बनाने के लिए संपीड़ित हवा का दबाव; - नोजल के माध्यम से पीपीएम प्रवाह दर; - सतह की दूरी; - धुंधला समय; - कोटिंग की मोटाई।
छोटे आइटम सेट (कारतूस) में पूरे किए जाते हैं और पूरे स्प्रे किए जाते हैं। छोटे उत्पादों को एक परत के साथ चित्रित किया जाता है और एक हाथ स्प्रे के साथ ज़िगज़ैग आंदोलनों का उपयोग किया जाता है। पीपीएम एप्लीकेशन चैम्बर्स चित्र 5 और चित्र 6 में दिखाए गए हैं।
एक ठंडा उत्पाद पर कोटिंग के दौरान होने वाले कोटिंग के दोषों को संपीड़ित हवा के साथ उड़ाने या संपीड़ित हवा के साथ उड़ाने के बिना अलग-अलग वर्गों को टिन करके लागू पाउडर सामग्री को हटाने के बाद उत्पाद को रंगकर समाप्त कर दिया जाता है।
एक गर्मी उपचार कक्ष में एक कोटिंग का गठन:
कोटिंग का गठन गर्मी उपचार कक्ष में 180 - 200 डिग्री सेल्सियस के तापमान पर 10-15 मिनट के लिए होता है। उत्पाद की सतह पर जमा पाउडर सामग्री उच्च तापमान से पिघल जाती है और अंतिम कोटिंग रूप लेती है। पॉलिमराइजेशन भट्टियों को 7 और 8 के आंकड़ों में दिखाया गया है।
परिवेश के तापमान (प्राकृतिक या बहती हवा) के लिए उत्पाद को ठंडा करना:कोटिंग की अंतिम प्रस्तुति शीतलन के बाद ही होती है। लेपित उत्पाद एयर-कूल्ड हैं। कोटिंग के गठन और इलाज के बाद, परिणामस्वरूप कोटिंग की उपस्थिति का गुणवत्ता नियंत्रण किया जाता है।
अंजीर। 5. स्प्रे बूथ - "Fig.6 के माध्यम से चलना"। स्प्रे बूथ - डेड एंड
अंजीर। 5.1 ITW गीमा स्प्रे बूथ
|
अंजीर। 5.2। एक बहुकोशिकीय के माध्यम से पुनरावृत्ति के साथ पाउडर परिसंचरण की योजना
Fig.5.3 प्लेट फिल्टर के माध्यम से पुनरावृत्ति के साथ पाउडर परिसंचरण की योजना।
स्प्रे बूथ (पाउडर कोटिंग उपकरण) है पाउडर कोटिंग उपकरण चित्रित उत्पादों पर इलेक्ट्रोस्टैटिक स्प्रे बंदूक।पाउडर कोटिंग बूथएक चक्रवात से सुसज्जित - धूल कलेक्टर और ठीक फिल्टर। उत्पाद पर जमा नहीं किया गया पाउडर पेंट एक चक्रवात - धूल कलेक्टर में जमा किया जाता है। ठीक चक्रवात धूल कलेक्टर के 99.8% तक ठीक होने के बाद हवा को फ़िल्टर करता है। स्प्रे बूथयह संपीड़ित हवा के लिए प्रकाश और कटौती प्रणाली से भी सुसज्जित है। स्प्रे बूथ और चक्रवात - धूल कलेक्टर का डिज़ाइन आपको किसी अन्य ब्रांड या पाउडर पेंट के रंग पर स्विच करने पर उन्हें जल्दी और कुशलतापूर्वक साफ करने की अनुमति देता है।
अतिरिक्त उपकरण:
चित्र 7। भाग मान्यता उपकरण
चैम्बर के प्रवेश द्वार पर - वर्कपीस की मान्यता - चौड़ाई, ऊंचाई, अंतराल और अंतराल - (एक प्रकाश बाधा या फोटोकेल के माध्यम से) और बंदूकों के आंदोलन का संगत समन्वय।
चित्र 7। पॉलिमराइजेशन फर्नेस "डेड एंड" अंजीर। 8। पॉलिमराइजेशन भट्टी "पास के माध्यम से"
पॉलिमराइजेशन भट्टी (पाउडर कोटिंग के लिए उपकरण) उत्पाद पर लागू बहुलक कोटिंग्स के पिघलने और पोलीमराइजेशन के लिए है।
कैमरा पोलीमराइजेशन भट्टियांयह एक डबल-इंसुलेटेड कंटेनर है जिसमें दोहरी दीवारें होती हैं, जिसके बीच का स्थान एक गैर-दहनशील गर्मी इन्सुलेटर से भरा होता है। भट्ठी कक्ष में हवा का मजबूर संवहन भट्ठी की पीछे की दीवार पर स्थित एक प्रशंसक द्वारा किया जाता है। पोलीमराइजेशन के दौरान उत्पन्न वाष्पशील गैसों को हटाने के लिए, पोलीमराइजेशन भट्टी निकास वेंटिलेशन और एक निकास छाता से सुसज्जित है। सिलोकेन घिसने पर आधारित एक विशेष प्रोफ़ाइल के साथ भट्ठी का द्वार सील करने से गर्मी के नुकसान को कम करने और भट्ठी की बिजली की खपत को कम करने में मदद मिली, जिससे महत्वपूर्ण ऊर्जा बचत हुई।
पाउडर कोटिंग पॉलिमराइजेशन फर्नेसइसमें विद्युत उपकरण हैं जो स्वचालित रूप से तापमान और पोलीमराइजेशन समय को बनाए रखता है। माइक्रोप्रोसेसर तापमान नियंत्रक और टाइमर का उपयोग आपको पॉलिमराइजेशन मापदंडों को जल्दी और आसानी से बदलने की अनुमति देता है। भट्ठी को परिवहन प्रणालियों और परिवहन उत्पादों के लिए परिवहन ट्रॉलियों से सुसज्जित किया जा सकता है।